A Guide to Ceramic Coated Elbows
Like what you’ve read? We have a digital version for you, give us your email below and we’ll send it to your inbox.
Utilizing our Guide to Ceramic Coated Elbows
This is your comprehensive guide to ceramic coated and ceramic lined elbows for your pneumatic conveying system. Whether you’re looking for an educational guide and general information about ceramic coating and ceramic lined elbows or you’re an pneumatic conveying professional needing more detail, you’ll find the information you need.
This ceramic elbow guide is useful for:
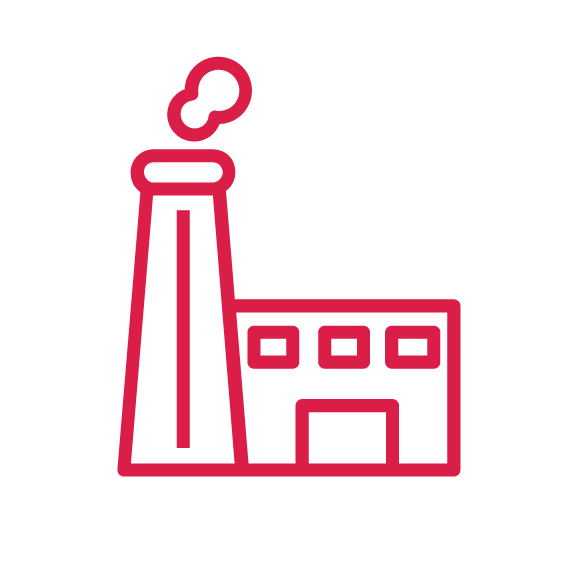
Manufacturers
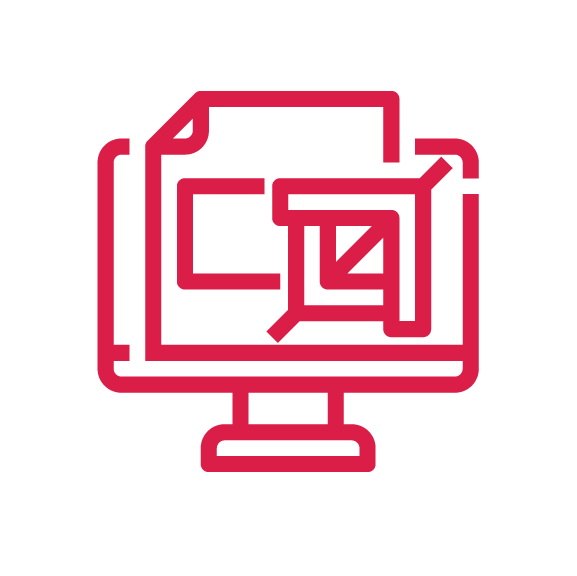
Designers and developers
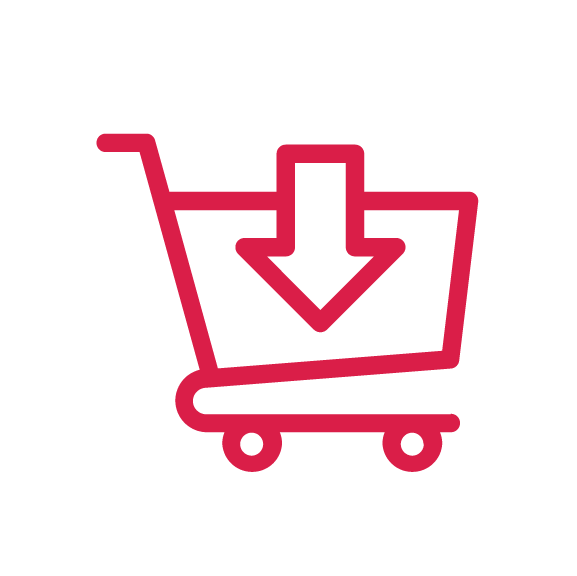
Purchasing engineers

Sales engineers
If you’re searching for new or replacement ceramic coated or ceramic lined elbows for your pneumatic conveying system, this guide also serves as a gateway to other relevant resources that will help you in your purchasing decision.
Navigate this Page
- What is ceramic coating in the context of pneumatic conveying?
- Why use ceramic coating?
- What does ceramic coating do in pneumatic conveying systems?
- Uses of ceramic coating in pneumatic conveying
- A history of ceramic coating
- Pros & cons of ceramic coatings
- Why you might need ceramic coated elbows
- Properties of ceramic coating in pneumatic conveying components
- How to order ceramic coated pipes and tubes
- Related content
What is ceramic coating in the context of pneumatic conveying?
Ceramic coating for elbows and other components of pneumatic conveying systems is intended to protect against abrasive wear, extending the life expectancy and reliability of these components.
Ceramic lined pipe elbows have relatively longer life expectancy because once the metal layer becomes worn by the abrasive action of particles, the ceramic layer takes over. Consequently, the following are achieved:
- Reduction in downtime due to repairs
- Productivity can be significantly improved
- Expenses are reduced
Some of the advantages of using ceramic-wrapped elbows and components, such as Ceram-BackⓇ elbows, include:
- Protection is provided where it is needed, namely on the back and sides of the elbow or high wear point on laterals, tees and wyes
- Provides excellent protection against all types of abrasion
- Ceramic coated elbows may also be used alongside other types of protection like induction hardening, porcelain lining, and tungsten carbide lining
- Any size, degree, or centerline radius of an elbow can be protected – ceramic coating is customizable
Why use ceramic coating?
Using ceramic coated elbows or ceramic coated fittings in a pneumatic conveying system will significantly increase its life expectancy. Ceramic coating helps protect pipes, elbows, and other fittings against abrasion from the material conveyed in your system.
Ceramic coating is customizable to your fittings which makes it great for adding extra protection on items that need to fit into a current system.
Once installed, the material will continue to flow through as before but once the metal wears out the material will then abrate against the much harder ceramic coating.
What does ceramic coating do in pneumatic conveying systems?
Ceramic coating is a thin protective layer that either lines or wraps around a pneumatic conveying elbow or a pipe or tube in your system.
It increases the durability and reliability of pneumatic systems because the wear and tear process on your components is minimized. As a result, downtime is reduced and productivity is optimized.
Some components of a pneumatic conveying system, like elbows, require the additional protection of a ceramic coating to minimize wear and tear. Ceramic coated elbows, for instance, are subjected to both impact and abrasive wear as the conveyed material changes direction inside these elbows.
Even at constant airspeed, material conveyed by a pneumatic conveyor does not have a perfectly consistent speed. When the sizes of the tubes change or particles turn in different directions, airspeed and pressure can also change.
The changes in airspeed and pressure also cause a change in how fast the material is traveling, and in some cases, turbulence occurs. These transition issues can cause damage to the components in your system. Abrasive friction can increase, particularly in the elbows, but ceramic coating can minimize extensive abrasion.
What is ceramic coating in pneumatic conveying used for?
Ceramic coating in pneumatic conveying systems is used either as an external or internal protective covering for elbows, fittings, pipes, and tubes. It protects against impact and abrasion.
Ceramic is used as a coating for:
Either applied externally or internally on the outside curve of the elbow, the areas most exposed to severe abrasion and impact
Ceramic coating is also applied to fittings that are exposed to mechanical stress and tension
Ceramic coating can be used in internally or externally line a chute or hopper
Industries that benefit from using ceramic coated elbows include:
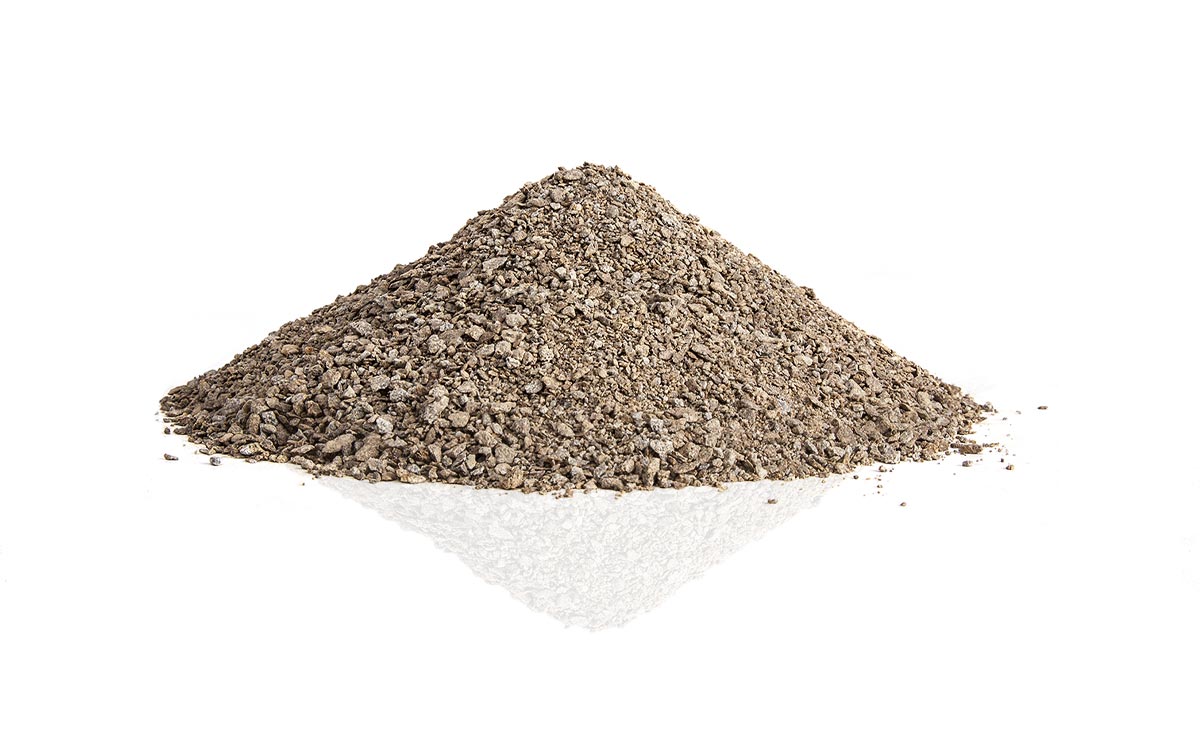
Due to the nature of materials conveyed in heavy industry, the main challenge here is abrasive wear on pneumatic conveying elbows
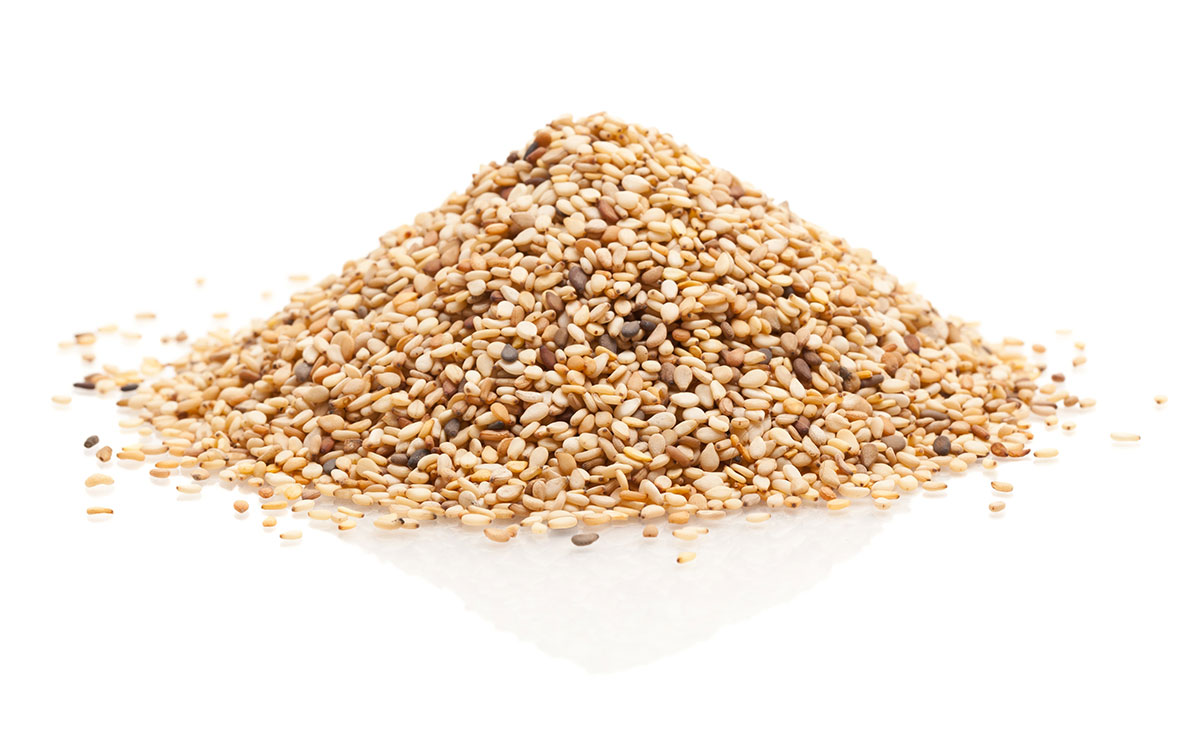
Using ceramic-coated elbows to convey grain helps to maintain quality and reduce the impact of abrasion
A history of ceramic coating
When we were founded in 1979, we had the aim of providing solutions to the process of wear and abrasion in pneumatic conveying systems because of friction and impact of particles – something that hasn’t changed to this day.
Tile-lined elbows were used by industries during that time as the main solution but it had several disadvantages and Bob Allison, founder of Progressive Products, saw and took the opportunity to improve the formulation of ceramic and the way it was used.
Bob was inspired by the ceramic tiles used by NASA to line the bottom of space shuttles as heat shields during re-entry in the atmosphere, and formulated a ceramic coating with similar properties to these tiles.
Since ceramic coating can be thinly applied, it can be used on any fabricated metal materials of any geometrical shapes. Decades later, the end result is our Ceram-BackⓇ elbow.
Pros & cons of ceramic coatings
Ceramic coatings are externally applied. This means that the interior metallic wall of an elbow, fitting or tube has to become worn first before the ceramic coating takes over the brunt of frictional abrasions from the particles being conveyed by the pneumatic conveying system. Here are some pros and cons of ceramic coatings as used in pneumatic conveying systems:
Pros
- Ceramic coating can be applied to any metal surface of any shape and size
- It provides excellent protection against sliding abrasion
- It is relatively inexpensive
- It is very reliable and helps reduce system downtime required for maintenance
- Ceramic lining and ceramic wrapping are very durable, meaning you will not have to replace components as often. Ceramic lining, in typical applications, will extend the life of the bare elbow or fitting by 8 – 10 times
Cons
- Heat limitations of up to 300 °F (149°C).
- Vulnerable to shear forces and stress fracture
- Not as good as ceramic tiles if you’re conveying large particles or have heavy impact
Learn more about the pros and cons of ceramic lined pipe elbows in pneumatic conveying systems.
Why might you need ceramic coated elbows?
If you have a pneumatic conveying system that conveys highly abrasive material such as grain, plastics, pet food, or chemicals and you don’t use any ceramic coating or ceramic lining, you’re probably finding that components in your system can easily wear. You might need frequent repairs and replacements, wasting time and money in the process. Ceramic coating or lining can help solve these problems.
Ceramic coated elbows are also very useful if you have several turns in your system. High-velocity particles that regularly change direction can easily damage elbows, and ceramic coating helps to protect them. The same goes for ceramic coated fittings, chutes, and hoppers.
Properties of ceramic coating in pneumatic conveying components
The exact physical properties of ceramic coating in pneumatic conveying components vary depending on the type of ceramic used, but some of the general properties of ceramic coatings are:
- Abrasion resistance
- High Mohs hardness
- Corrosion resistance
- Moisture resistance
- Some are also impact resistant
Some of the most common types of abrasion-resistant ceramic coatings used in pneumatic conveying are:
- Silicon carbide
- Boron nitride
- Cerium oxide
- Aluminum oxide
- Titanium dioxide
- Silicon dioxide
Ready to place ceramic coated pipes and tubes in your pneumatic conveying system?
If you’re searching for a new supplier, it’s good to know how to go about ordering ceramic coated or ceramic lined pipes and tubes, and what questions to ask that will ensure you get the right components for your system.
Some of the specifications that you’ll need to know are:
Degree of bend • Pipe or Tube diameter • Wall thickness • Type of metal • What ends are required (plain, flanged, Victaulic, etc.)
A sales engineer can help you determine the type of coating that is right for your system. The type of backing needed for your system will vary due to type of system, material conveyed among others.
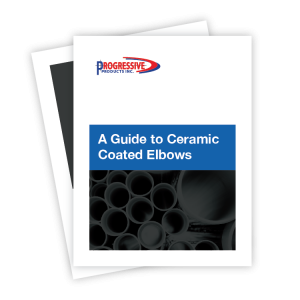
Download Our Guide to Ceramic Coated Elbows Now!
If you like what you’ve read, we have a PDF version you can take with you.